An SOP is a Standard Operating Procedure that describes how an organization should operate in order to achieve its goals. An SOP is usually written down and distributed among all employees so everyone knows exactly what to expect.
Standard operating procedures (SOPs) are step-by-step instructions documented by an organisation to make sure that services and products are delivered to a set standard, every time. SOPs are a vital component of all Quality Systems.
SOPs can help you evaluate what you are doing now as well as assist with decision-making for the future.
Here are 5 easy steps to creating an effective Standard Operating Procedure:
Define what it means to have an effective SOP.
Having an effective SOP is essential to running any business efficiently. If there isn’t one, then employees will not know what to do when faced with a situation that requires them to perform a task. This can lead to confusion and mistakes.
Identify the purpose of the SOP.
Before creating an SOP, it is helpful to identify its purpose.
- Is it meant to help employees understand how to complete tasks more effectively? or
- Does it simply provide guidelines for completing certain tasks?
If the expectation within the organization is that everyone must follow the same rules, then it must be clear what those rules are. The easiest way to do this is to document them.
Determine who will use it.
Once you have determined what the SOP should accomplish, determine who will use it.
- Will it be used by everyone in the company? or
- Just by some people?
If it is only going to be used by one department, then it might not be necessary to write one at all.
Make sure your SOP is being written for the right reasons.
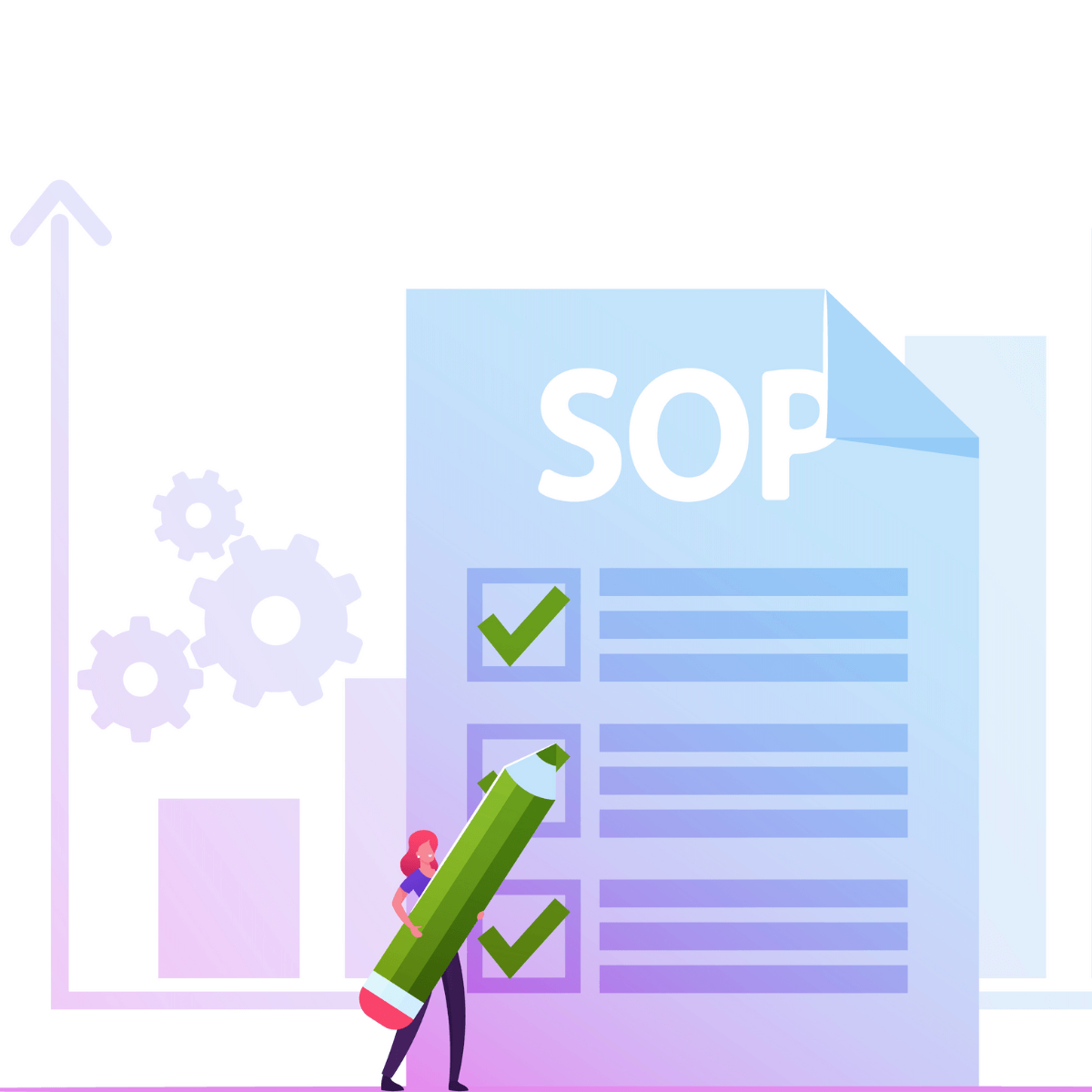
Create a draft. Include any relevant information.
After determining who will use it, write down the steps needed to complete each task. This includes things like how to perform the task, what tools and resources will be required, and where the materials and information will come from.
Review the draft with the team.
Once you have written out the steps, review them with the rest of the team. Make sure everyone understands the process and has input into the final version.
SOPs must provide consistency – the more consistent a process, the less chance there will be quality problems. As long as each individual within the team performs the task as they are written, there is a greater chance of reducing errors.
Consumers trust products manufactured using consistent quality processes and specifications. SOPs specify steps that help standardize these processes and, therefore, quality.
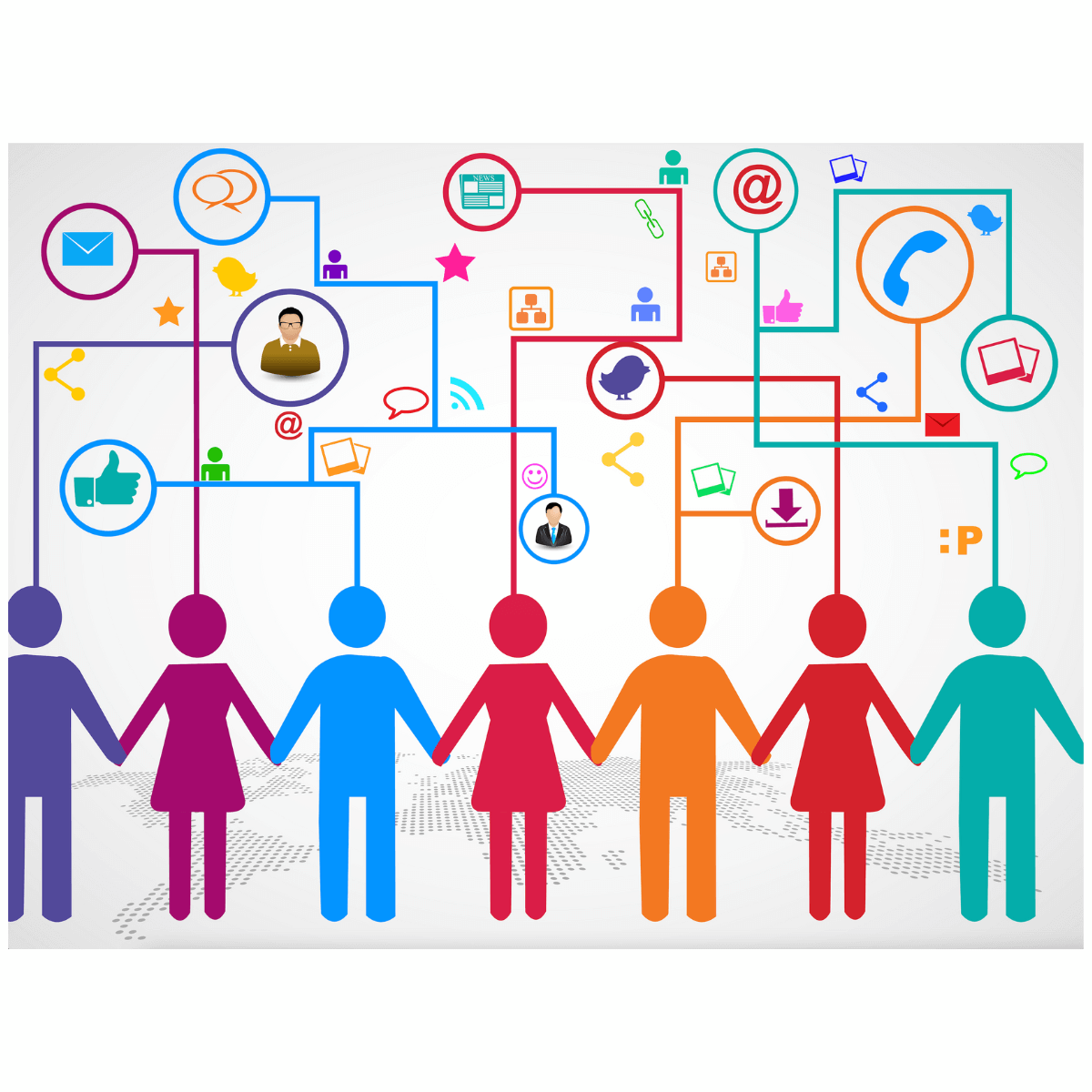
A well-written SOP can ensure that you have a structured quality system and processes in place, trained and qualified employees, as well as an encouraging company culture.
Want a free SOP template?
Sign up to our resources page and download your free sample template.
Want to know how our training can help achieve your SOP goals?
See our comprehensive range of food safety and quality assurance courses. Our fun, in-person classes as well as our live, expert-led online training courses are council-approved and suitable for all businesses operating in the food sector. If you think your company could benefit from additional staff training, contact us for more information.